Современная
промышленность давно уже в состоянии выпускать самые разнообразные по свойствам
и составам стали. И некоторые из них вполне можно использовать для изготовления
клинков ножей. К сожалению, в нашей стране «специальные клинковые» стали, в
промышленных объемах не выпускают. А тут еще такие требования… Как быть добросовестному изготовителю?
Можно добывать
правдами и неправдами вожделенные «отрезы». А можно и
самому создавать необходимый клинковый материал. Вот несчастные
производители малосерийной или штучной продукции и крутятся в надежде угодить
потребителю и заработать на хлеб, желательно с маслом. Но этим благим попыткам
сильно мешают законы физики.
Ведь для того
чтобы нож хорошо резал и долго держал заточку, он должен быть закален до
высокой твердости. Однако, тут же всплывает иная неприятность — сталь при
закалке, набирая твердость, теряет свою упругость. Повышаем упругость отпуском
клинка? И тут же снижаем твердость… Углеродистые стали имеют более качественный
рез, но быстро ржавеют, порой приводя владельца в исступление.. Нержавейки
выглядят пресно и бедно рядом с красавцами — дамасками и булатами. Круг проблем
кажется неразрывным, но человек уже давным-давно научился эти трудности
преодолевать, через что и слывет «существом достаточно разумным».
И были им
изобретены составные, то есть, композитные клинки…
Конечно,
побудительным мотивом к такому устройству клинков у древних служил поначалу
бесконечный дефицит, дороговизна хороших сталей. Потому и начали ее совмещать
на клинке с простым железом. Добротный металл ставили именно на лезвие, убивая,
таким образом, сразу нескольких саблезубых зайцев. И сталь экономили, и прочную
режущую кромку получали. Да и прочность на излом-изгиб становилась повыше.
Соответственно новому качеству продукции рос и авторитет кузнецов, способных
такое сотворить. Да и кошелек пополнялся быстрей.
Дальше —
больше.
Неистощимая
фантазия наших предков, подстегиваемая насущной необходимостью, привела к
изобретению целой массы способов и технологий для обмана законов физики и
улучшения материального положения рабочего класса. Попытаюсь эти способы и
технологии описать.
Кузнецы
древней Руси применяли пять основных технологических приемов в изготовлении
ножевых клинков:
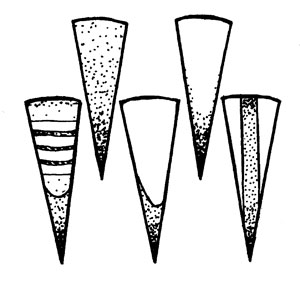
1.Сварка клинка ножа из трех
полос: в середине стальная, а по бокам железные.
2.Наварка стального лезвия на
железную основу клинка.
3.Комбинированная сварка:
узорчатое составное из нескольких пластин стали и железа тело клинка, стальное лезвие и железный обух.
4.Цементация железного клинка.
5.Ковка цельностального клинка.
(последние два способа к
композитным клинкам не относятся).
Японские
кузнецы применяли сходные техники, но со своими особенностями.
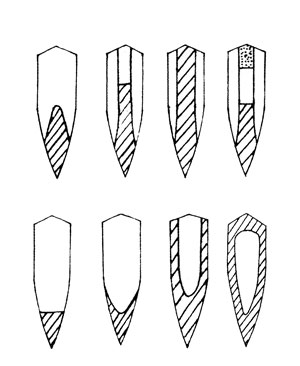
Так, мягкий сердечник они
оборачивали твердой сталью.
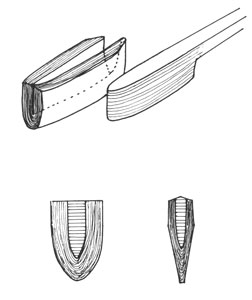
Или изготавливали сложносоставные
клинки из нескольких частей (тоже, в свою очередь, многослойных) с разным
содержанием углерода и различным расположением волокон.
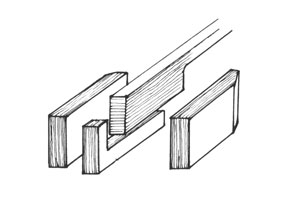
Применяли они и зонную закалку, —
при помощи специальных обмазок покрывали клинок, и где толщина обмазки была
меньше (на лезвии), там сталь закаливалась сильнее и имела большую твердость.
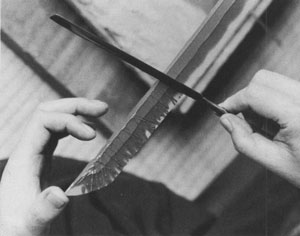
В целом,
кузнецы различных стран и эпох имели свои любимые конструкции и способы
получения клинков. Общее в подходах было одно — все они направлены на повышение
эксплуатационных свойств клинка, а в дальнейшем — и для повышения
декоративно-художественных свойств изделия.
Ну, а как
обстоят дела с композитами в клинковом производстве сегодня?
Давайте
узнаем. Современные композиционные материалы можно разделить на четыре основные
группы:
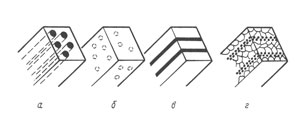
1.Волокнистые материалы, то есть
композиты, состоящие из волокон прочного материала, распределенных в более
вязкой матрице (а);
2.Дисперсно-упрочненные
материалы, состоящие из матрицы с равномерно распределенными в ней дисперсными
частицами твердых и высокопрочных фаз (б);
3.Слоистые материалы,
представляющие собой чередующиеся слои пластичного и прочного компонентов (в);
4.Естественно-композиционные
материалы, получающиеся путем направленной кристаллизации эвтектических сплавов
или направленного формирования эвтектоида (г).
Ко второй группе
можно отнести современные кобальтовые и титановые сплавы типа Talonite высокая
стойкость режущей кромки клинка которых обеспечивается выделениями сверхтвердых
карбидов, выступающих в роли «микропилы»…
Но основное
внимание мне хочется уделить рассмотрению именно третьей группы слоистых композитов, как наиболее интересных
для производителя штучной продукции..
Начнем с
минимума слоев — с трех.
Эта технология
известна издревле, но распространение и возможности современных материалов
заставили взглянуть на нее с надеждой на новые перспективы...
Какого улучшения
свойств помогает добиться такая компоновка клинка? Использование мягкой
нержавеющей стали для наружных слоев (обкладок) и высокоуглеродистой, с
великолепными режущими свойствами стали для центрального слоя, позволяют
получить клинок, мало подверженный коррозии. Получить клинок, обладающий более
качественным резом, нежели простые нержавейки. Этот клинок будет практически
невозможно сломать в ходе эксплуатации, ведь мягкие обкладки играют роль своеобразного
демпфера, удерживающего от излома твердый, центральный слой. Такой клинок
просто согнется. И это не радует? Что же, он сможет быть опять выправлен...
Согласитесь, что это куда как предпочтительный вариант, чем невеселая
перспектива остаться с обломком клинка из моностали один на один с дикой
природой… Не на заднем плане стоит и фактор экономии качественной
высоколегированной стали, ведь толщина центрального слоя составляет всего 1-2
мм.
Самая «модная» в
последние годы российская сталь для этого слоя (как и цельных клинков) это
Х12МФ. Содержащиеся в ней 1,4-1,6% углерода и 11-12,5% хрома позволяют добиться
получения клинков с хорошей режущей способностью и высокой стойкостью к износу
и затуплению. Помимо эксплуатационного «позитива» есть и еще такое немаловажное
обстоятельство, — эту сталь практически невозможно термообработать плохо, она
терпима к ошибкам в закалке и отпуске. За что ее иногда и называют — «ленивой
сталью». Лично же мне
интереснее работать со сталью Х12.
Являясь сталью
ледебуритного класса с содержанием углерода до 2,2%, она (по своему химическому
составу) стоит ближе к чугунам или к булатам. С последними ее роднит и
«булатоподобный» узор на полированной поверхности, ясно видимый после травления
слабой кислотой.
На обкладки
можно поставить практически любую сталь или композит, здесь все определится
личной фантазией и техническими возможностями мастерской. В ход и идет все,
начиная от мягкой «пищевой нержавейки» и
20Х13, до всевозможных дамасков, включая нержавеющие. Получаются очень колоритные
графические решения. Высокая декоративность дамасских обкладок подчеркивается
суровой рабочей простотой твердого центрального слоя.
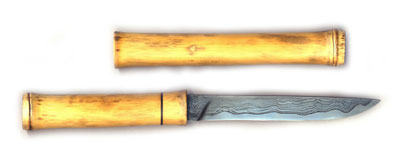
И вот что еще
важно…
Если в
древности на первый план выходили рабочие характеристики клинка, от которого
часто зависела сама жизнь владельца, то сегодня потребителю нужно, чтобы сам
нож был еще и красивым, а порой просто пафосным… В качестве примера «красивой
высокосвойственной трехслойки» я приведу такой вариант — цветной дамаск
обкладок и булатный центральный слой! Или вот так — простые, но абсолютно
нержавеющие обкладки и сверхтвердая, режущая стекло (но подверженная коррозии)
порошковая сталь мастера Петрика из Краснодара. Или его же «пузырьковая» сталь.
Простор для подобных экспериментов просто безграничный!
Но самый яркий
и характерный представитель замечательного класса слоистых композитов —
дамасская сталь.
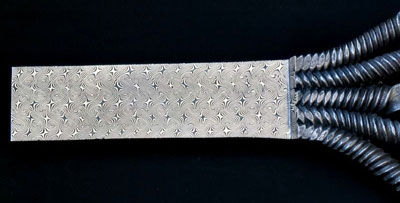
Для
изготовления дамаска применяются разные стали — инструментальные,
конструкционные, коррозионностойкие… Железо, никель, другие цветные металлы… в составе
дамаска одним из компонентов может быть даже булат!
В основном
потоке практической работы пока применяются углеродистые стали. Это неизбежно
провоцирует развитие коррозии на клинке. Однако, убедительных данных, говорящих
о чрезмерном и сверхбыстром ее образование из-за разности электрических
потенциалов в слоях (как говорят некоторые) не существует.
Дамасская
сталь различается по типу используемых материалов, по способу получения и по
рисунку. Являясь, в том числе, и общепризнанным «художественным композитом»,
дамаск имеет и ряд действительно уникальных свойств. Чередование волокон стали,
получивших после термообработки высокую твердость и хрупкость с волокнами стали
мягкой, но упругой, образуют на режущей кромке «микропилу».
И, чем слоев
больше, тем «микропила» мельче.
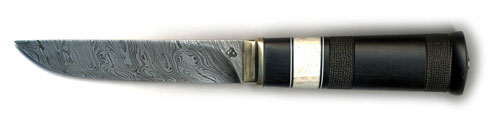
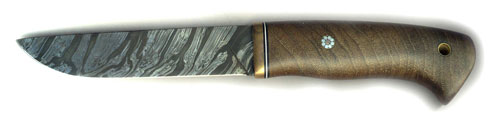
Это свойство
дамаска и обуславливает его повышенные режущие свойства. Оно создает эффект,
который можно очень условно назвать «самозатачиваемостью». Конечно, такой нож
не точит сам себя (как порой думает пользователь), но мягкие волокна его
клинка, срабатываясь быстрее, обнажают более твердые участки, — нож при работе
дольше сохраняет свою способность хорошо резать. Здесь понятия «микропилы» и
«самозаточки», по существу, являются одним и тем же явлением.
Хрупкость
стали, получившей после закалки высокую твердость, компенсируется упругостью
слоев мягких. Такие клинки выдерживают большие динамические нагрузки на изгиб.
Ну, и немаловажную, а подчас и главную роль играют изумительные декоративные
свойства дамасского узора! Способов получения этого узора существует великое
множество, — от относительно простых, до самых сложных, требующих высокого
уровня мастерства.
А есть еще и
«Вечная Легенда»…
Булат — сталь,
получаемая различными методами, связанными с полным или частичным расплавлением
исходного материала.
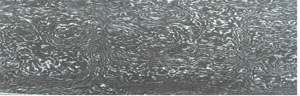
И, если дамаск
— это сталь, полученная методом кузнечной сварки, то булат — это тигельная
(литая), высокоуглеродистая, с особыми свойствами сталь. В основе строения
булатной стали лежит естественная дендритная кристаллизация с большими
разновидностями протекания процесса.
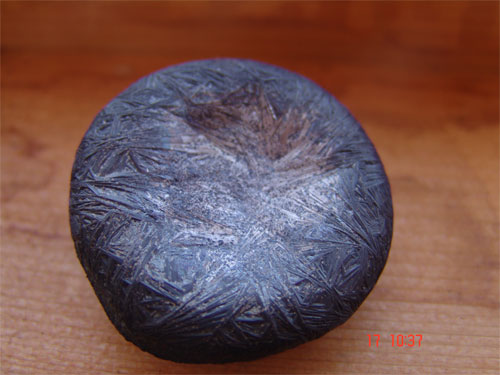
В структуре булата есть те же
составляющие, что и в обычной стали: феррит, перлит и цементит, но они в корне
отличаются своим строением и расположением.
Булат так же
различается по типу используемых материалов, по способу получения и по рисунку,
но здесь уже и сам рисунок несет в себе информацию о свойствах этого
великолепного материала.
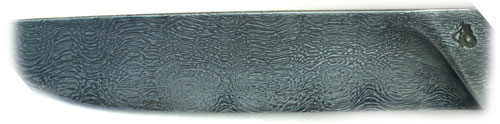
Количество
углерода в булате — от 0,8% до 3%. В последнее время уже получены булаты с
различными легирующими добавками, повышающими их эксплуатационные свойства. В
частности, добавка хрома позволяет получить коррозионностойкий булат.
А к какому
классу композитов отнести булатную сталь?
Вот что пишут
в своей монографии «Булатная сталь» В.А. Щербаков и В.П. Борзунов: «На наш
взгляд, булатную сталь нельзя отнести к волокнистым композитам. Во-первых, в
булатной стали связь между сверхвысокоуглеродистыми волокнами и
низкоуглеродистой матрицей реализована на основе одинаковой кристаллической
решетки железа, а положение границы раздела «волокно-матрица» изменяется в
процессе высокотемпературной пластической деформации вследствие изменения
сечений волокон, их конфигурации и контрастности. Нельзя исключать и обратного
процесса при эксплуатации изделий из булатной стали. Во-вторых, температура
плавления объемов сверхвысокоуглеродистых волокон булатной стали ниже
температуры плавления матрицы. В-третьих, физико-механические свойства
составляющих композита типа булатной стали формируются в процессе получения и
эксплуатационные свойства композита не являются результатом только сформированной
композиционности.
Булатную сталь
нельзя отнести к группе композитов, включающей дисперсно-упрочненные материалы.
Во-первых, в композитах типа булатной стали отсутствует равномерное
распределение упрочняющих частиц (выделений вторичного цементита) по объему
композита в целом, напротив, повышенные эксплуатационные свойства булатной
стали достигаются в большой степени благодаря созданной макронеоднородности, в
том числе и в распределении выделений вторичного цементита. Во-вторых, в основе
отличительных признаков булатной стали лежит анизотропия различных
свойств, что не характерно для композитов рассматриваемой группы.
Булатную сталь
нельзя отнести также и к группе композитов, включающих слоистые материалы.
Во-первых, сейчас во многом очевидно, что строгая слоистость в булатной стали в
принципе бы не позволила реализовать возможную совокупность сверхсвойств этого
композита и сама «строгость» недостижима в технологии производства настоящей
булатной стали. Во-вторых, именно кривизна сверхвысокоуглеродистых волокон формирует
в локальных объемах булатной стали необходимые характерные градиенты упругих
напряжений, воздействующие на те или иные процессы и явления.
И наконец, булатную
сталь, по-видимому, нельзя отнести к так называемым естественным композиционным
материалам. Во-первых, булатная сталь ни в волокнах, ни в прослойках матрицы не
содержит эвтектики, которая могла бы существенным образом повысить прочностные
свойства композита. Во-вторых, повышенные эксплуатационные свойства булатной
стали достигаются не в результате существования двух состояний одной фазы,
например высокоуглеродистого и низкоуглеродистого мартенсита. В-третьих,
настоящая булатная сталь обладает в отличие от естественных композитов
совершенно иной, более высокой, энергетикой и состояние металла в составе
булата далеко не естественное и требует колоссальных затрат внешней энергии для
его достижения. Более того, в отличие от других композитов формирование
булатной стали сопровождается беспрецедентной аккумуляцией внешней прилагаемой
энергии.
На наш взгляд,
булатная сталь должна быть выделена в особый класс композитов».
Мнение
специалистов лишний раз подчеркивает уникальность булата, как клинкового материала.
И эта потенциальная уникальность притягивает внимание многих экспериментаторов,
старающихся освоить выпуска булата. В последнее время участились попытки найти
единый, универсальный рецепт получения булата в домашних условиях, как
говорится, буквально «на коленке». Полученный таким образом узорчатый металл
дал основание некоторым исследователям достаточно поспешно сделать вывод о
разгадке тайны булата, да и вообще об отсутствии этой тайны как таковой. Порой
выводы излишне безапелляционны.
Очень жаль, но
уже стало «хорошим тоном» плюнуть в сторону П.П.Аносова и смело заявить о
полном непонимании им сути процесса получения булата и «случайности и
нерегулярности» результатов его опытов…
Однако,
смельчаки как-то забывают о том, что Аносов наладил на Златоустовском заводе
промышленный выпуск клинковых изделий из булата, и этот булат соответствовал
лучшим сортам старинного восточного… А режущие и прочностные характеристики
узорчатых металлов, полученных этими «исследователями новой формации» остаются
полной загадкой для пользователей и коллег. По переписке результат не оценишь,
однако… блеклый и крайне невыразительный узор большинства подобных образцов
очень уж показателен!
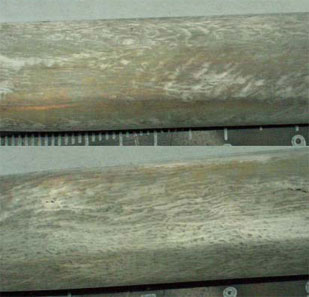
Достаточно
сравнить его со старинными, даже среднесортными и низшими булатами и разница
становится очевидна!
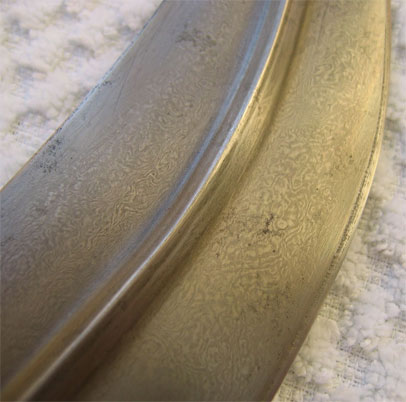
Приводится множество громких метафор и ссылок на
иностранные авторитеты, однако… в подобной продукции нет главного! — крупного,
четкого, гроздевидного с коленами узора.
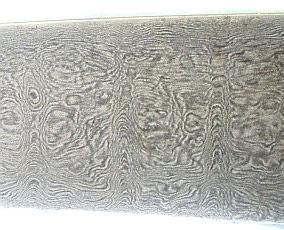
Ведь именно узор говорит о свойствах
булата, и именно по форме узора в древности судили, хорош конкретный булат или
нет.
Попытки же
изобразить процесс плавки булата в виде памфлетных комиксов для всех подряд,
включая детей и беременных женщин, крепко попахивают откровенным «шаманством» и
искусственной профанацией идеи.
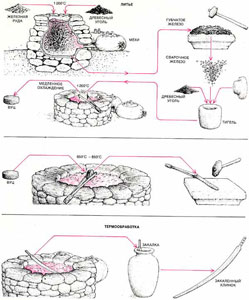
Ведь мало
просто отлить булатный слиток, нужно его правильно термообработать, а потом
определенным (а не абы как!) образом выковать клинок, правильно его закалить и
отпустить, и правильно протравить… Именно
правильная ковка придает львиную долю легендарных свойств булатному клинку.
Причем, малейшая ошибка на любом этапе этого процесса ведет к получению совсем
другого результата, чаще всего с ухудшением свойств. А самое
главное — надо продемонстрировать весь набор рабочих свойств ножа с клинком из
такого вот «булата»! Показать все его возможности, прибегнув к помощи коллег и
опытных пользователей. Но этого не происходит, идет просто погоня за «узором» в
самой абстрактной, лишенной всякой жизненности и прикладной ценности фазе…
Именно сейчас
булаты переживают второе рождение, ренессанс, если хотите. И, если мы не хотим
в ближайшее будущее увидеть все «прелести» профанации интереснейшей технологии,
не хотим получить «валовый булат» без всяких свойств и качеств, захлестнувший
ножевые прилавки, как, в свое время, это случилось с «черными дамасками», то
стоит проявить выдержку и разумную осторожность. Ждать не новых споров, а новых
практических результатов. И отзывов
пользователей.
Самих
рецептов, способов и технологий получения булата существует множество, как и
сортов и видов самого булата, а открывать и узнавать их всем нам предстоит еще
долго. Однако, надо признать, что общие принципы же давно ясны и не составляют
никакого секрета…
Просто есть
тонкости. Они пока ускользают от новоявленных первооткрывателей.
Но ведь кроме
дьявола, еще и само Чудо кроется именно в мелочах.
В тех самых
мелочах, с помощью которых мы и сможем удивить и порадовать владельца отличного
ножа из композитных материалов.